Industrial Chemical Pumps in Singer, LA
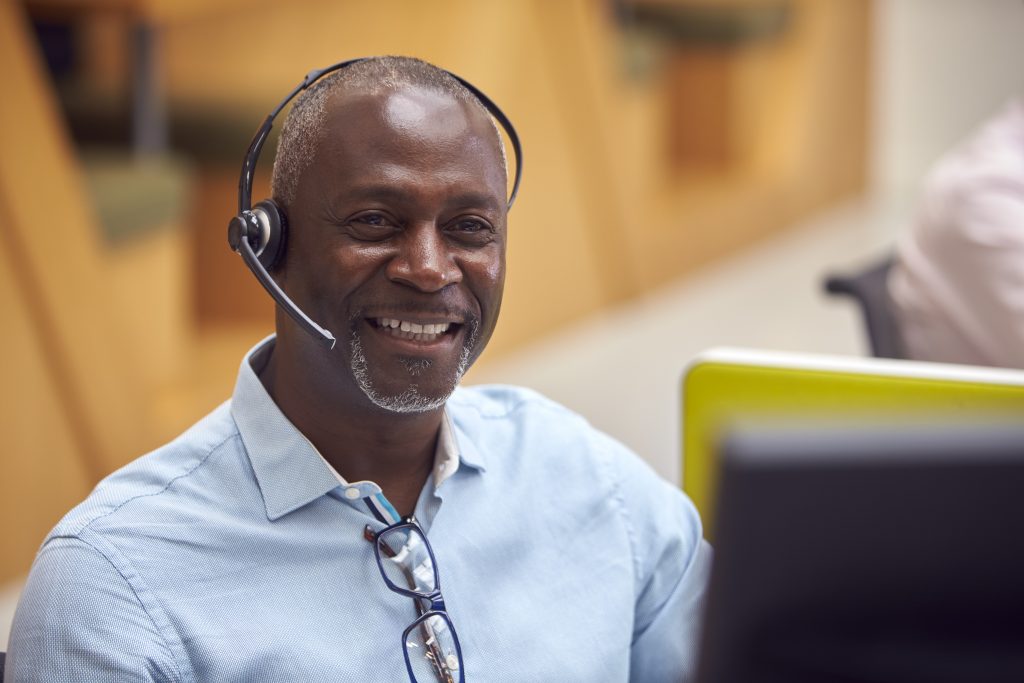
Singer Small Centrifugal Pumps
Centrifugal pumps' high flow rates and capacity to handle large volumes of fluid are two of their main advantages. Additionally, they have a fairly simple design that is simple to maintain. Applications for Centrifugal pumps include water treatment, irrigation, oil & gas production, and chemical processing. Centrifugal pumps come in a variety of designs, including axial, mixed, and radial flow pumps. Each type has its own distinct set of qualities and is created for particular applications.
Singer LA Drum Pumps
Drum pumps are used for a wide range of commercial, industrial, and residential applications which all involve moving liquids from large drums or containers to other locations where the liquid is required. This includes transferring liquids such as water, oil, gasoline, and various other types of chemicals and liquids. Additionally, drum pumps can be used to dispense fluids in specific amounts, making them practical for filling containers and for uses in manufacturing.
Drum Pumps are popular in industries such as mining, agriculture, and manufacturing. Chemical processing industries rely on drum pumps for things like food proccesing and pharmaceuticals. Even water treatment and construction industries use drum pumps as drums are a regular container in these industries.
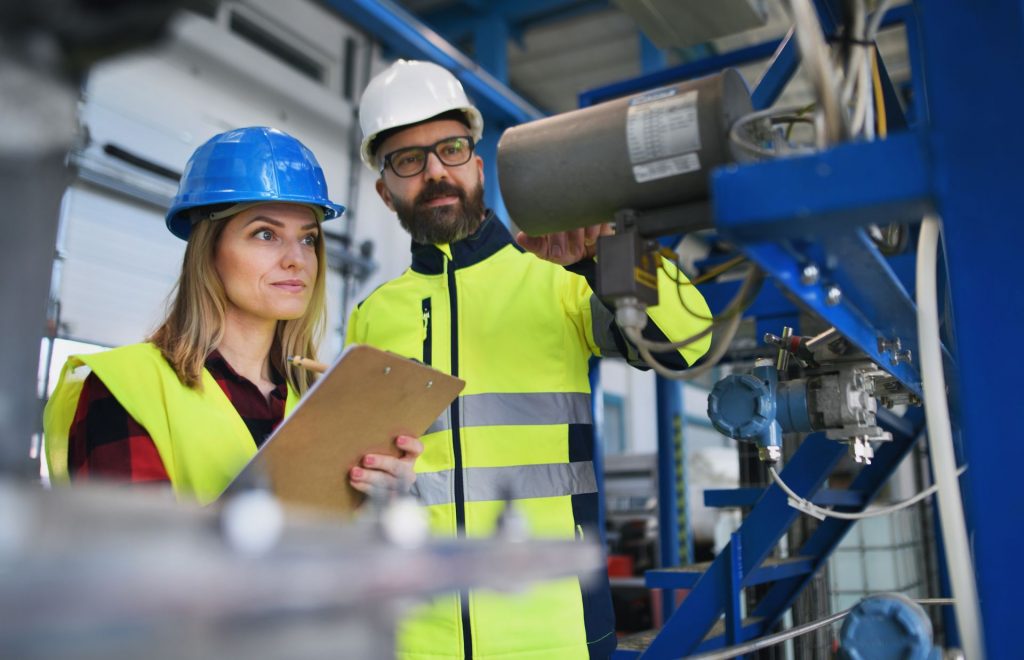
Singer, LA Small Centrifugal Pumps and How They Work
Centrifugal pumps use a rotating impeller to move fluid through a system. This impeller, which is a disk with vanes or blades attached to it, is driven by a motor and the rotation exerts a centrifugal force that causes the fluid to move away from the center of the disk. Due to the difference in pressure caused by this movement, the fluid is drawn into the pump and moved through the system. In addition to transferring fluids, these pumps can be utilized to transport gases.
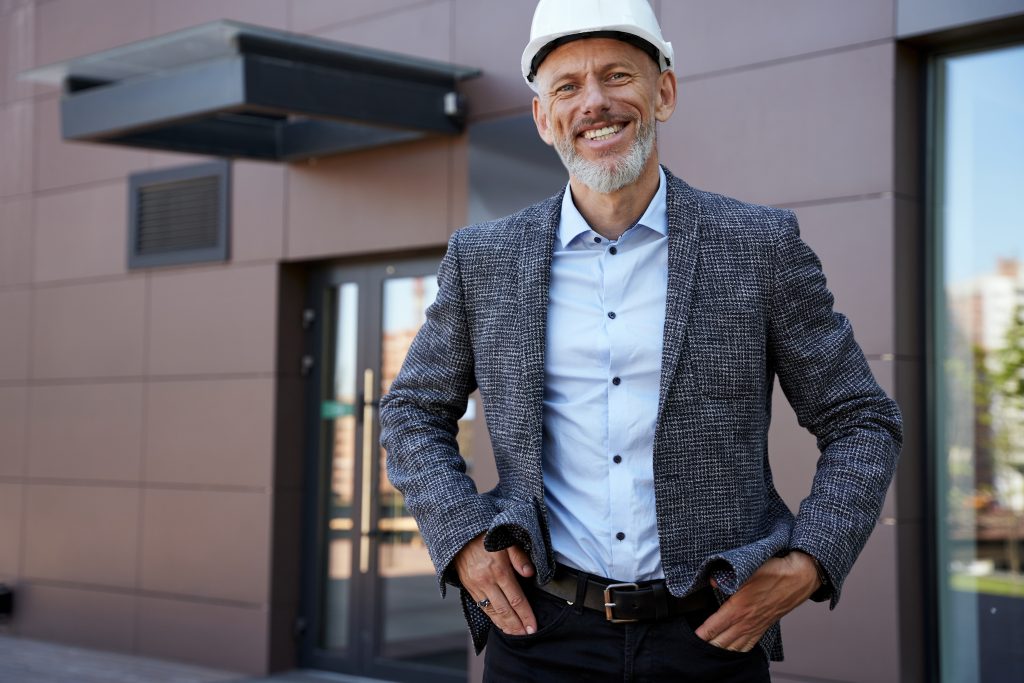
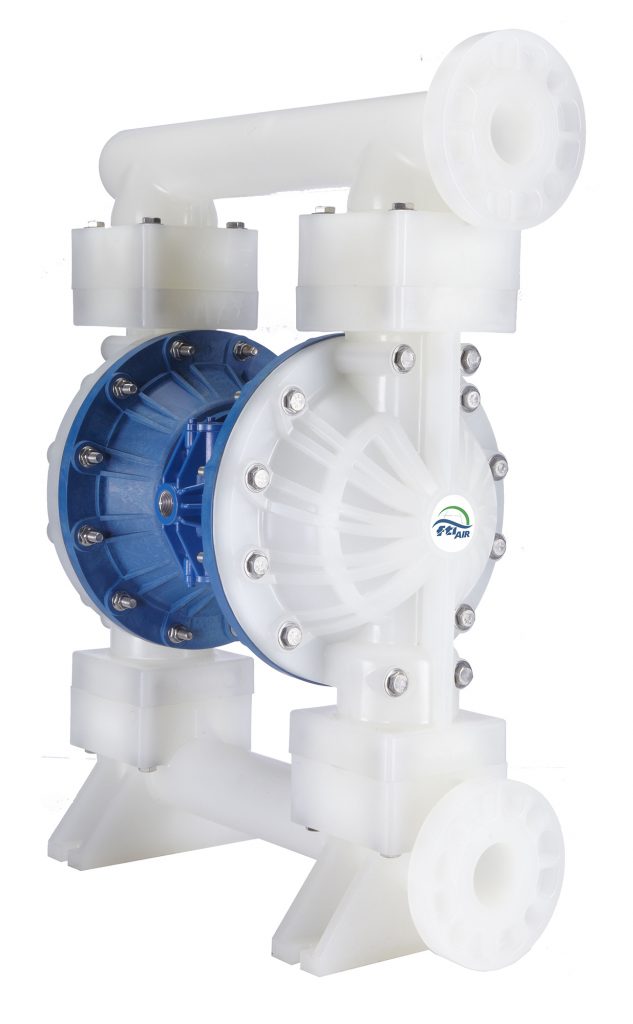
Singer Air-Operated Diaphragm Chemical Pump Designs & Their Advantages
Fluid-handling devices that employ air pressure to transfer fluids include air operated diaphragm chemical pumps. They are available in several designs, including single- and double-diaphragm models, ball valve layouts, and nonmetallic wetted component setups. These pumps are adaptable and reasonably priced. They can tolerate caustic or abrasive fluids, have high flow rates, and can prime themselves.
They can be used even if the liquid levels change because they are self-priming and can run dry without causing damage. Additionally, they require relatively little maintenance and can deliver a constant flow rate. Last but not least, because these pumps are air-operated, they are simple to install and use a small amount of electricity.
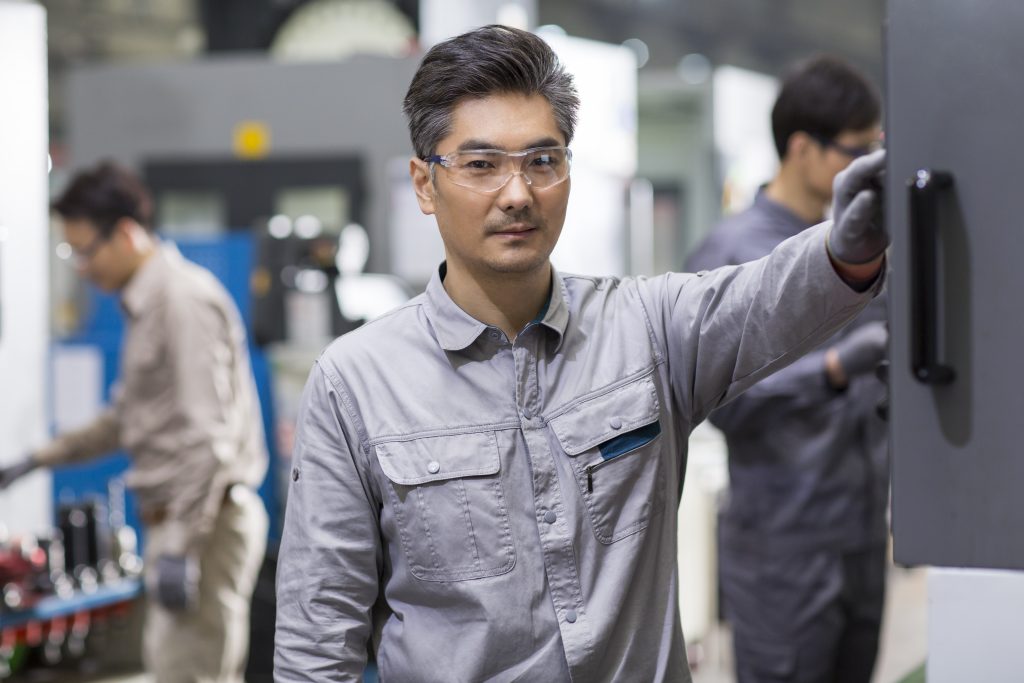
MSDB SERIES - MAGNETIC DRIVE, SEALLESS, Singer CENTRIFUGAL PUMPS
- High specific gravity handling – over 1.8
- Maximum working pressure up to 135 PSI (9.3 bar)
- Minimum flow rate is 1 gpm (.23m3/h)
- High power neodymium magnetic drive system handles high specific gravity fluids
- Two stage versions contain two impellers, three stage versions contain three impellers
- Horizontal or vertical (with IEC motor only) installation
- Heads up to 300 feet (91.5m)
- Compact close-coupled design
- Engineered for corrosive fluids with polypropylene/Ryton© or PVDF/Ryton© construction
- Sealless design improves reliability with no seal maintenance to perform or seal leaks
Choosing the Correct Drum Pump in Singer LA
When selecting the ideal drum pump for a specific use, there are several factors that should be taken into account. These factors include:
- Size and weight: Take into account the size and weight of both the pump and the drum or other container from which you will be transferring the liquid. Verify that the pump can fit inside the drum and is not too heavy to handle.
- Compatibility with the medium being transferred: Different models of drum pumps are specifically designed to handle different types of liquids. It is crucial to select the pump that is compatible with the type of liquid you need transported, as some liquids or chemicals can be too abrasive or viscous to work with certain models.
- Price: Establish your spending limit and select a pump that satisfies your requirements at a cost you are comfortable paying.
- Volume and flow rate: Consider both the volume and flow rate of the liquid you need to move. Ensure that the drum pump you select has a flow rate that meets your requirements.
- Power source: Choose a pump that will meet the demands of your application and the type of power source you have available.
- Safety considerations: Pick a pump that complies with applicable safety regulations and is suitable for the unique dangers prevalent in your application. Make sure the pump is explosion-proof, for instance, if you are transporting explosive liquids.
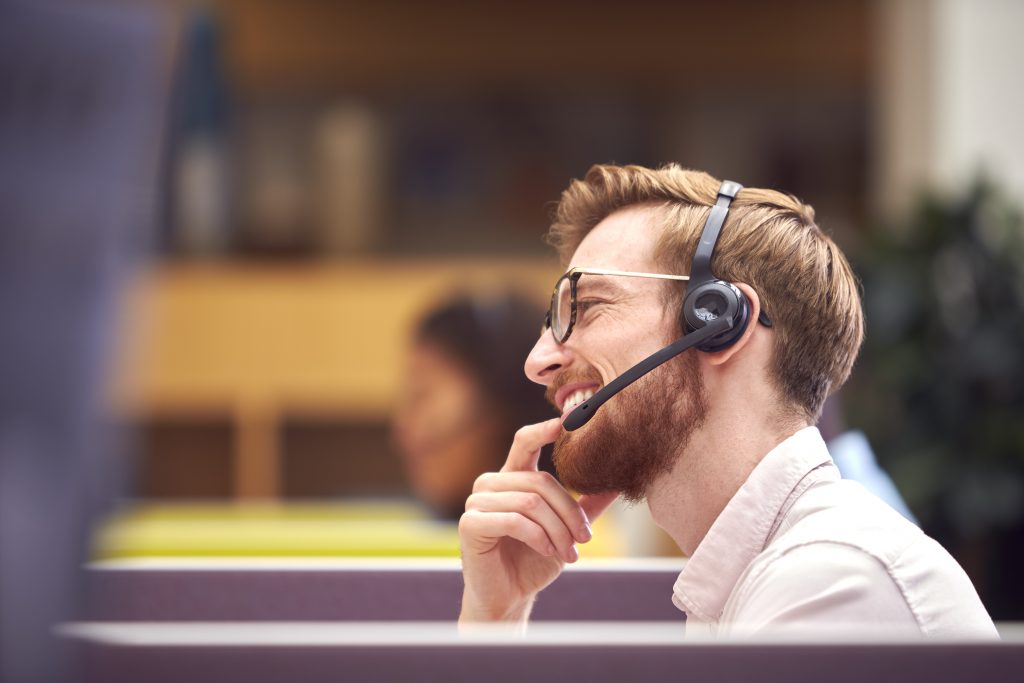