Industrial Chemical Pumps in Wakefield, MI
Wakefield, MI Small Centrifugal Pumps and How They Work
Centrifugal pumps use a rotating impeller to move fluid through a system. This impeller, which is a disk with vanes or blades attached to it, is driven by a motor and the rotation exerts a centrifugal force that causes the fluid to move away from the center of the disk. Due to the difference in pressure caused by this movement, the fluid is drawn into the pump and moved through the system. In addition to transferring fluids, these pumps can be utilized to transport gases.
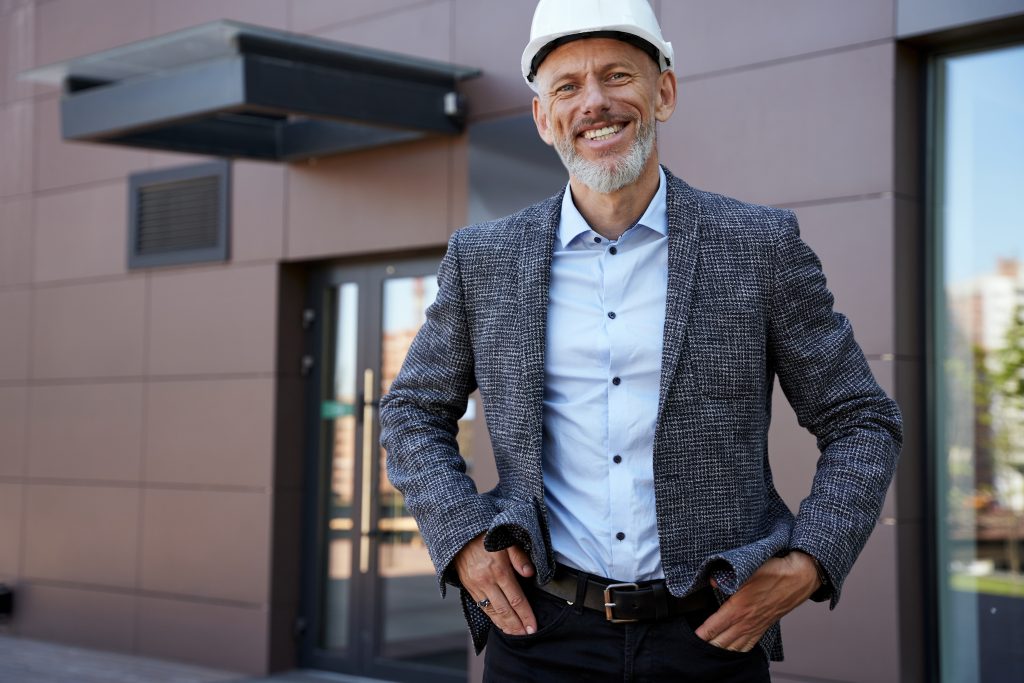
Small Centrifugal Pumps in Wakefield, MI
High flow rates and capacity to handle large volumes of fluid!
Wakefield, MI Drum Pump Accessories
- Cycle Counter - The FTI Air Cycle Counter is an electronic device that counts pump cycles by detecting the presence of the valve carrier. The cycle counter can be universally used on any new or existing FTI Air pump with the proper air valve components.
- AODDampener - AODDampener is unique pulsation dampener manufactured from 316L stainless steel with PTFE backed diaphragm, has fully automatic air control and handles a wide variety of applications.
- SPILLSTOP - Fully pneumatic system safely captures leaked product due to diaphragm failure and automatically shuts down failed pumps to eliminate costly product loss and prevent hazardous spills.
- Pulsation Dampeners - Removes virtually all hydraulic shock while producing a near steady flow of fluid. Protect piping, valves and fittings from destructive pulsations and surges. Available in a wide range of materials of construction
- Filter/Regulator - Compact, integrated design saves space and reduces piping, includes dual scale psi/Bar gage. Filters incoming air to five microns. Regulator adjusts air pressure from 7.3 to 120 psi (.5 to 8.3 bar).
- Liquid Level Control - The FTI Liquid Level Control is a pneumatic/mechanical device that will automatically turn the pump on and off as the liquid level changes
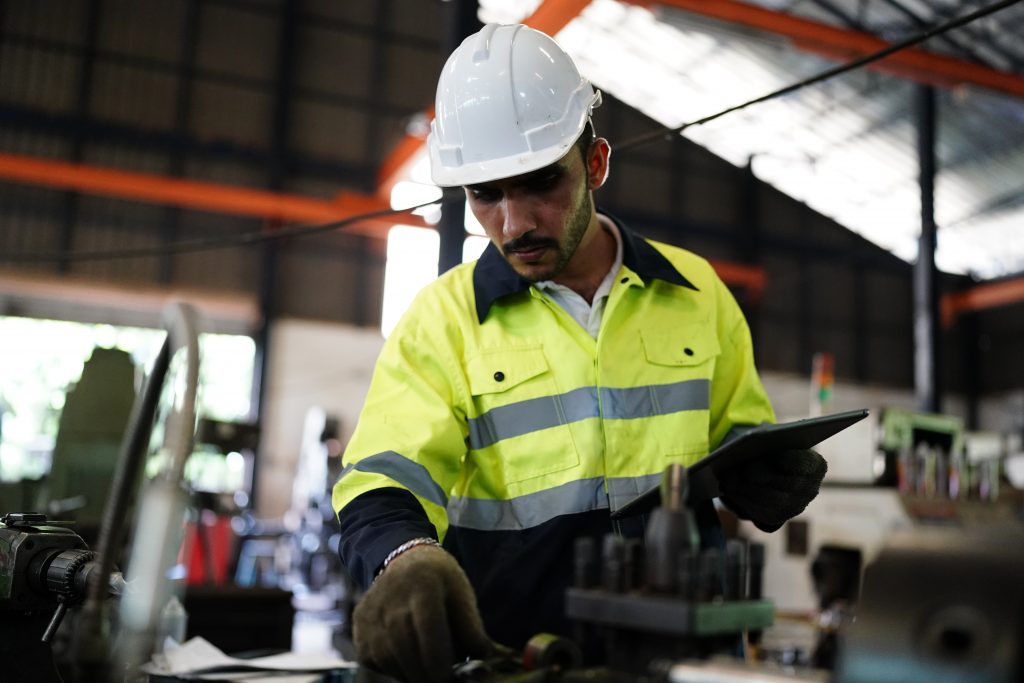
Choosing the Correct Drum Pump in Wakefield MI
When selecting the ideal drum pump for a specific use, there are several factors that should be taken into account. These factors include:
- Compatibility with the medium being transferred: Different models of drum pumps are specifically designed to handle different types of liquids. It is crucial to select the pump that is compatible with the type of liquid you need transported, as some liquids or chemicals can be too abrasive or viscous to work with certain models.
- Price: Establish your spending limit and select a pump that satisfies your requirements at a cost you are comfortable paying.
- Size and weight: Take into account the size and weight of both the pump and the drum or other container from which you will be transferring the liquid. Verify that the pump can fit inside the drum and is not too heavy to handle.
- Safety considerations: Pick a pump that complies with applicable safety regulations and is suitable for the unique dangers prevalent in your application. Make sure the pump is explosion-proof, for instance, if you are transporting explosive liquids.
- Volume and flow rate: Consider both the volume and flow rate of the liquid you need to move. Ensure that the drum pump you select has a flow rate that meets your requirements.
- Power source: Choose a pump that will meet the demands of your application and the type of power source you have available.
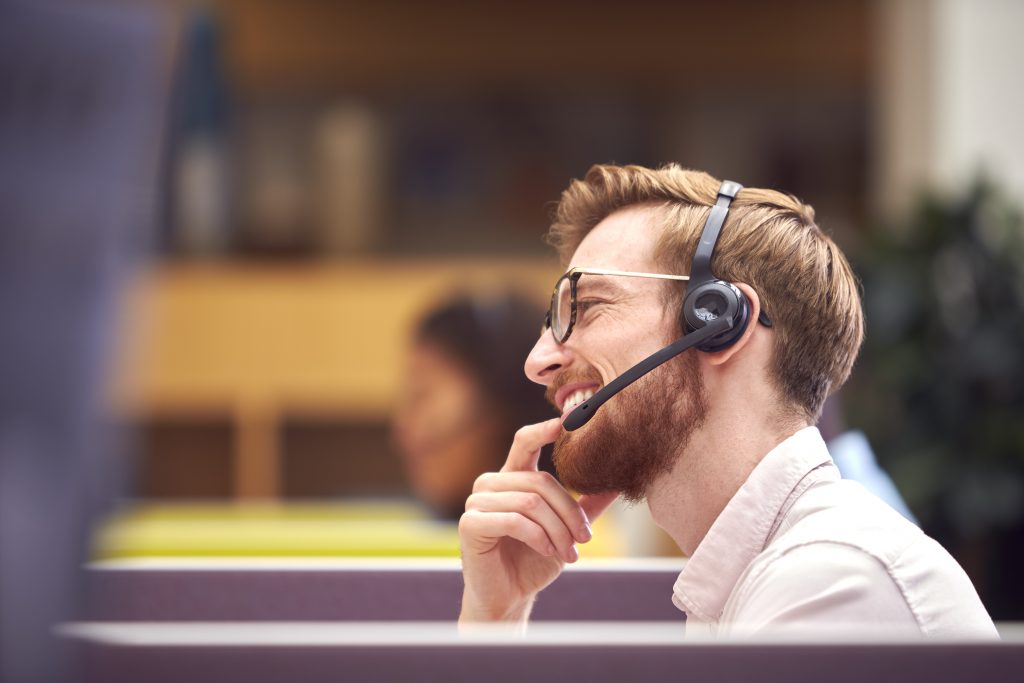
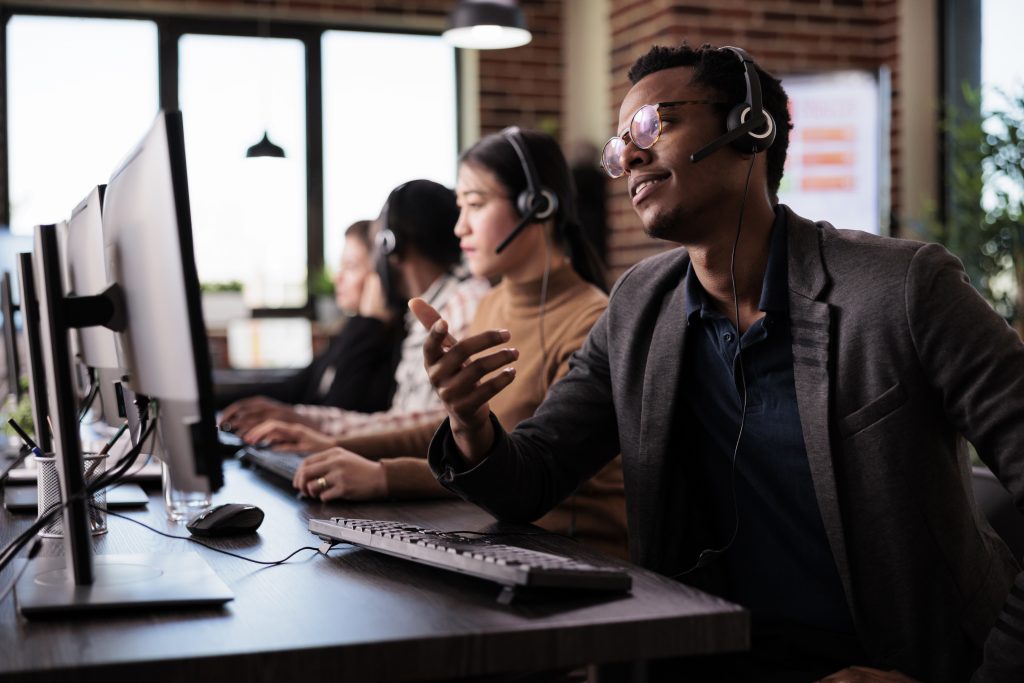
Wakefield Small Centrifugal Pumps
Centrifugal pumps' high flow rates and capacity to handle large volumes of fluid are two of their main advantages. Additionally, they have a fairly simple design that is simple to maintain. Applications for Centrifugal pumps include water treatment, irrigation, oil & gas production, and chemical processing. Centrifugal pumps come in a variety of designs, including axial, mixed, and radial flow pumps. Each type has its own distinct set of qualities and is created for particular applications.
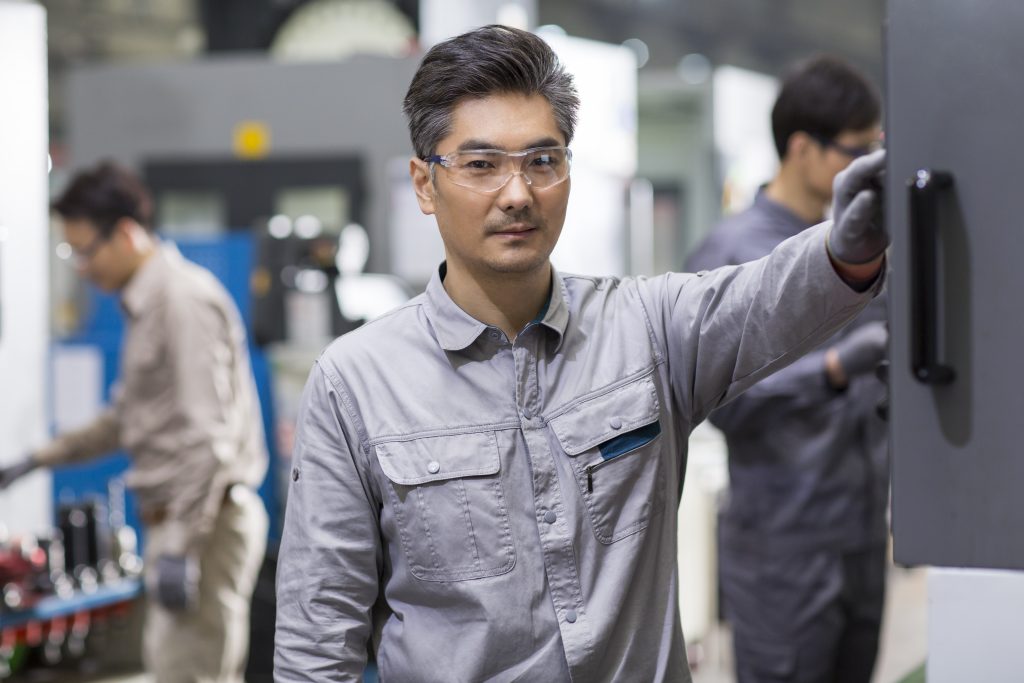
MSDB SERIES - MAGNETIC DRIVE, SEALLESS, Wakefield CENTRIFUGAL PUMPS
- Two stage versions contain two impellers, three stage versions contain three impellers
- High power neodymium magnetic drive system handles high specific gravity fluids
- Sealless design improves reliability with no seal maintenance to perform or seal leaks
- Compact close-coupled design
- Minimum flow rate is 1 gpm (.23m3/h)
- Engineered for corrosive fluids with polypropylene/Ryton© or PVDF/Ryton© construction
- Heads up to 300 feet (91.5m)
- High specific gravity handling – over 1.8
- Horizontal or vertical (with IEC motor only) installation
- Maximum working pressure up to 135 PSI (9.3 bar)