Industrial Chemical Pumps in Ridgefield, IL
Ridgefield IL Drum Pumps
Drum pumps are used for a wide range of commercial, industrial, and residential applications which all involve moving liquids from large drums or containers to other locations where the liquid is required. This includes transferring liquids such as water, oil, gasoline, and various other types of chemicals and liquids. Additionally, drum pumps can be used to dispense fluids in specific amounts, making them practical for filling containers and for uses in manufacturing.
Drum Pumps are popular in industries such as mining, agriculture, and manufacturing. Chemical processing industries rely on drum pumps for things like food proccesing and pharmaceuticals. Even water treatment and construction industries use drum pumps as drums are a regular container in these industries.
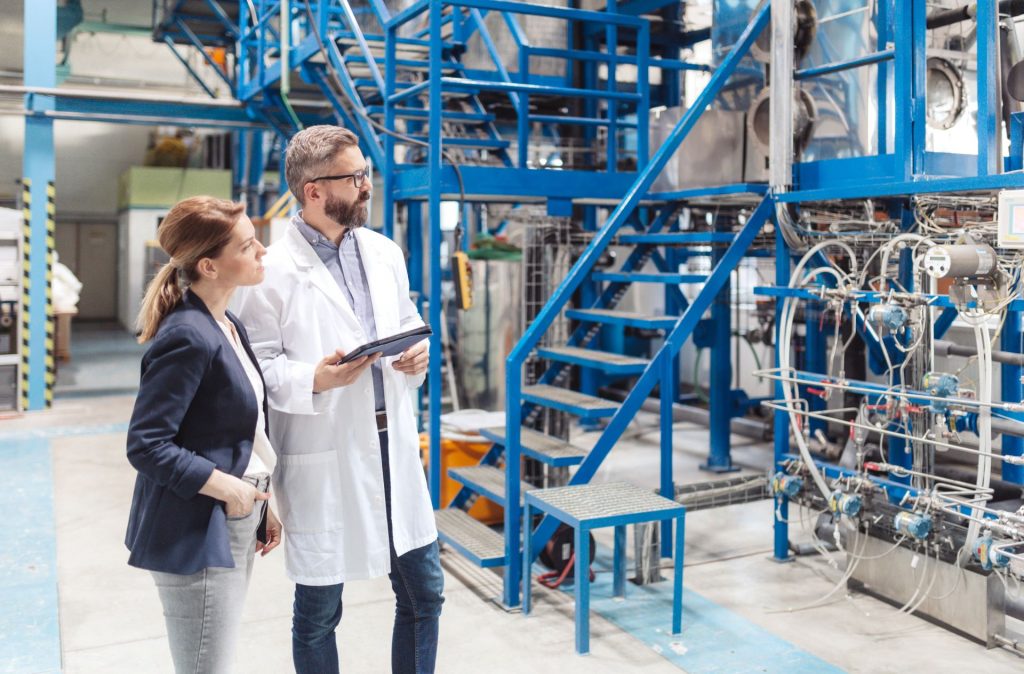
Ridgefield Air-Operated Diaphragm Chemical Pump Designs & Their Advantages
Air Operated Diaphragm Chemical Pumps are a type of fluid-handling equipment that uses air pressure to move fluids. They come in different designs, such as single- and double-diaphragm models, ball valve designs, and nonmetallic wetted part constructions. These pumps are relatively affordable and versatile. They have high flow rates, can prime themselves, and can handle fluids that are abrasive or corrosive.
One key benefit is that they are self-priming and can run dry without damage, meaning they can be used even if the liquid levels fluctuate. Also, they can provide a steady flow rate with very little maintenance. Finally, since these pumps are air operated, they are easy to install and require minimal electricity usage.
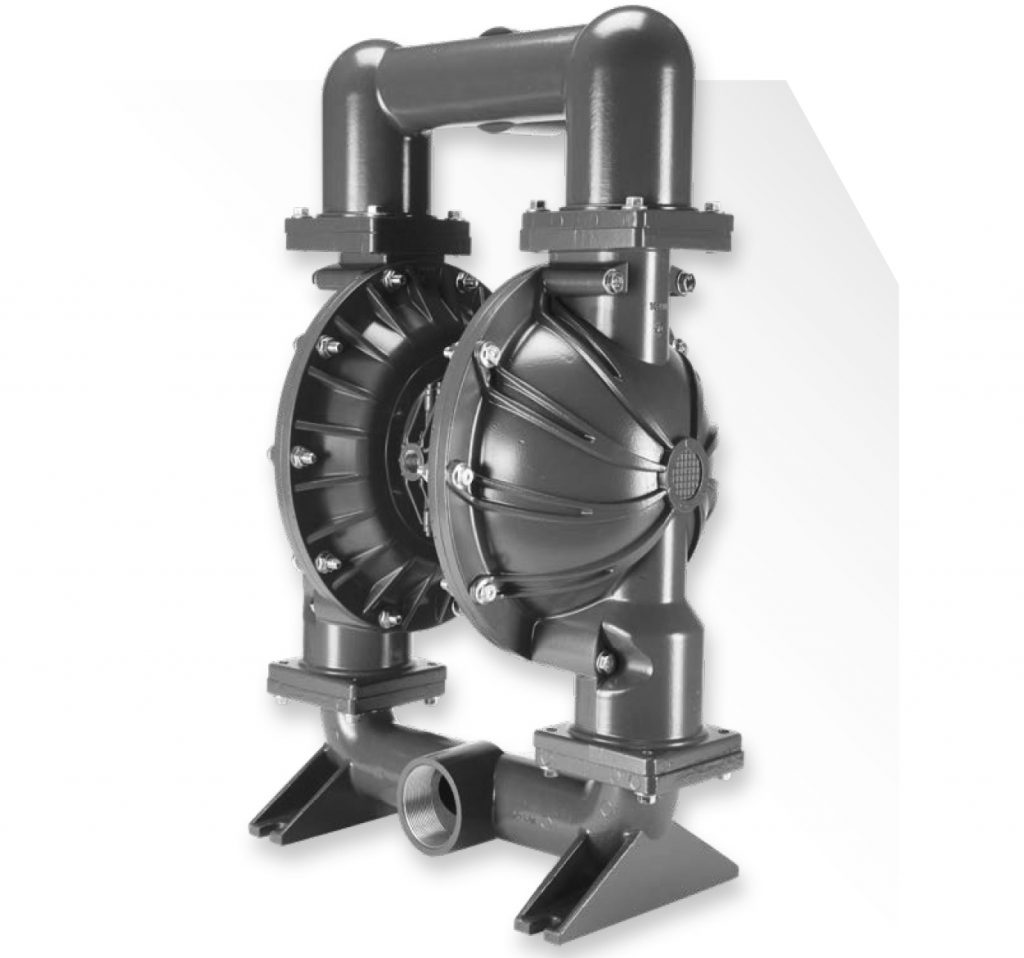
Air-Operated Diaphragm Chemical Pumps are Durable, Reliable, and Easy to Maintain
These pumps can move a wide range of chemicals, both acidic and alkaline, reliably and with the least amount of maintenance. Because they are powered by air, they can be used in dangerous places because they can't explode and don't have any electrical parts. Air-Operated Diaphragm Chemical Pumps are long-lasting and reliable pieces of equipment that can be used for a long time in harsh conditions.
Not only do these pumps need little maintenance, but they also have a system of air valves that keeps the flow rate and pressure consistent. They work well to move a wide range of chemicals without the need for priming or lubrication. Air Operated Diaphragm Chemical Pumps are very easy to maintain, making them an ideal choice for many chemical applications.
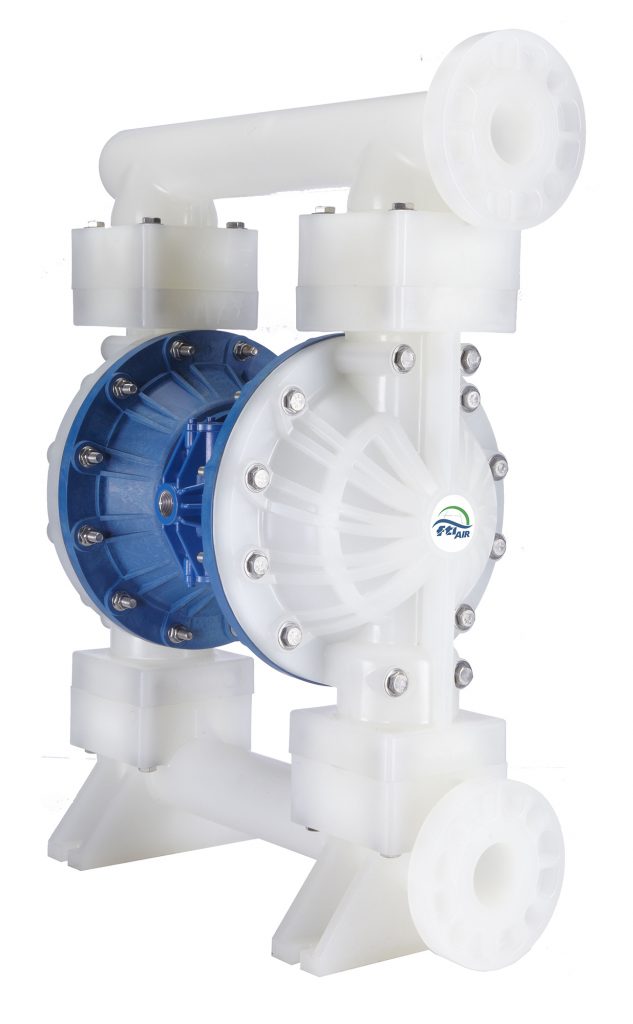
Ridgefield Air-Operated Diaphragm Chemical Pump Designs & Their Advantages
Fluid-handling devices that employ air pressure to transfer fluids include air operated diaphragm chemical pumps. They are available in several designs, including single- and double-diaphragm models, ball valve layouts, and nonmetallic wetted component setups. These pumps are adaptable and reasonably priced. They can tolerate caustic or abrasive fluids, have high flow rates, and can prime themselves.
They can be used even if the liquid levels change because they are self-priming and can run dry without causing damage. Additionally, they require relatively little maintenance and can deliver a constant flow rate. Last but not least, because these pumps are air-operated, they are simple to install and use a small amount of electricity.
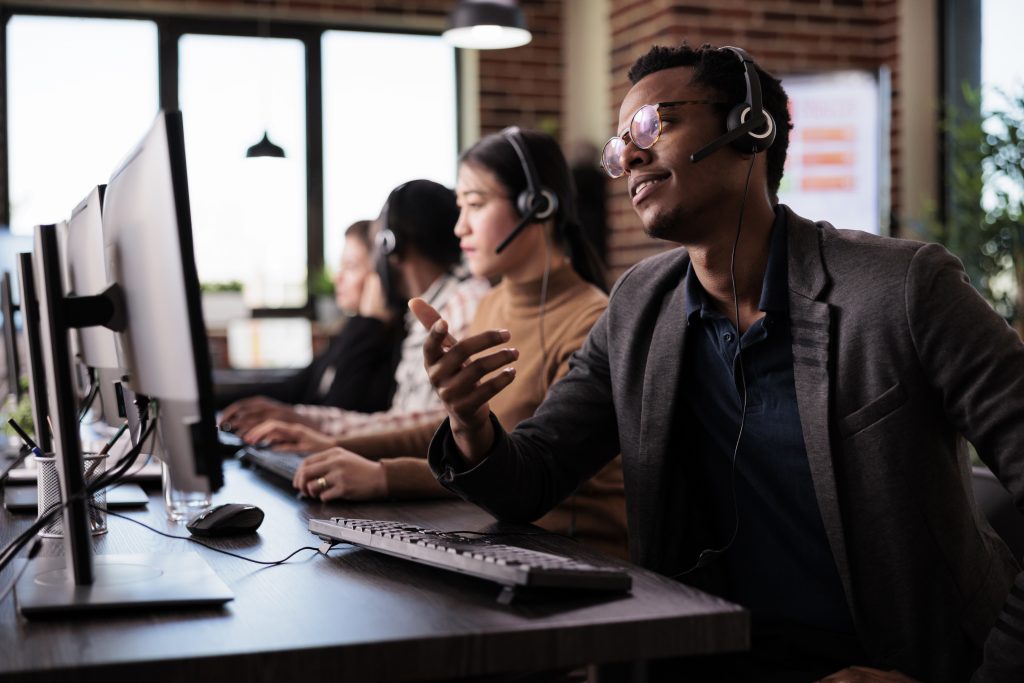
Ridgefield Small Centrifugal Pumps
Centrifugal pumps' high flow rates and capacity to handle large volumes of fluid are two of their main advantages. Additionally, they have a fairly simple design that is simple to maintain. Applications for Centrifugal pumps include water treatment, irrigation, oil & gas production, and chemical processing. Centrifugal pumps come in a variety of designs, including axial, mixed, and radial flow pumps. Each type has its own distinct set of qualities and is created for particular applications.
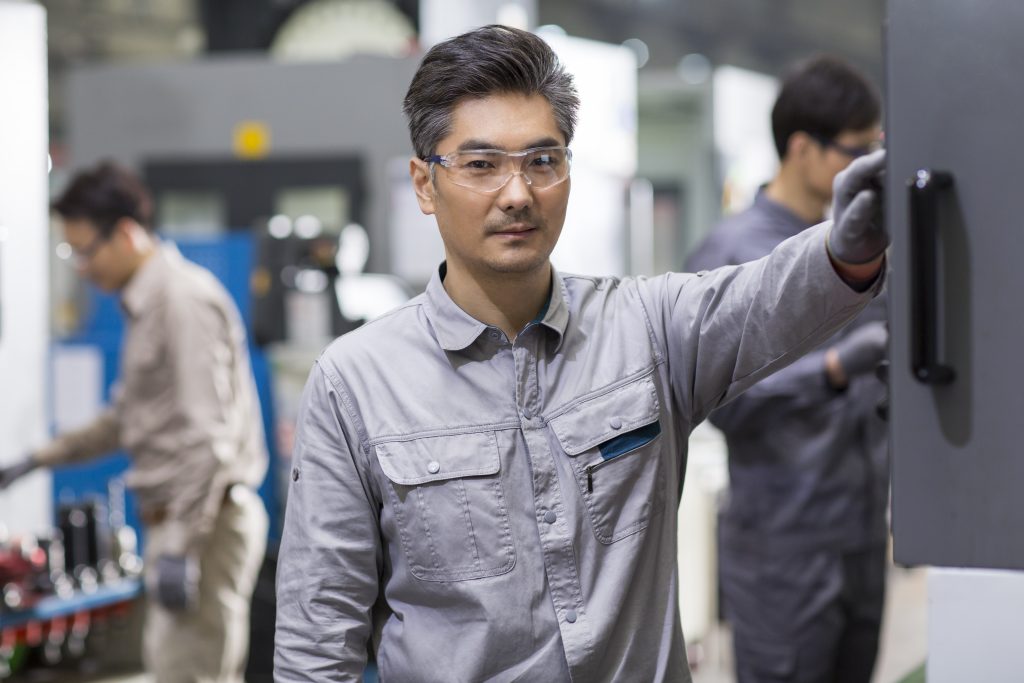
MSDB SERIES - MAGNETIC DRIVE, SEALLESS, Ridgefield CENTRIFUGAL PUMPS
- Two stage versions contain two impellers, three stage versions contain three impellers
- Horizontal or vertical (with IEC motor only) installation
- High specific gravity handling – over 1.8
- Sealless design improves reliability with no seal maintenance to perform or seal leaks
- High power neodymium magnetic drive system handles high specific gravity fluids
- Minimum flow rate is 1 gpm (.23m3/h)
- Heads up to 300 feet (91.5m)
- Engineered for corrosive fluids with polypropylene/Ryton© or PVDF/Ryton© construction
- Compact close-coupled design
- Maximum working pressure up to 135 PSI (9.3 bar)